What is Vacuum Pressure Testing?
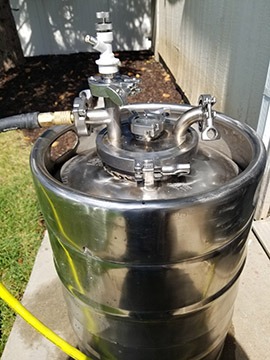
Vacuum pressure testing is a non-destructive testing method used to determine the presence of leaks or defects in a sealed system. This method involves lowering the pressure inside a sealed system to create a vacuum, and then monitoring how the system responds. By testing for leaks or defects under vacuum conditions, any potential issues can be identified before the system is put into use.
How Does Vacuum Pressure Testing Work?
Vacuum pressure testing works by creating a vacuum within a sealed system and then monitoring changes in pressure over time. Here's a step-by-step breakdown of how the process typically works:
1. Preparation – Before vacuum pressure testing can begin, the system being tested must be thoroughly cleaned and prepared. This includes removing any debris or contaminants that could affect the accuracy of the test.
2. Sealing – The system being tested is then sealed to create an airtight environment. This can involve using seals or gaskets, welding or soldering seams, or other methods of ensuring a tight seal.
3. Evacuating – The air inside the sealed system is then evacuated using a vacuum pump or similar device. This creates a vacuum inside the system, with the pressure dropping to a predefined level.
4. Monitoring – Once the vacuum has been created, the system is monitored for any pressure changes over time. If the system is airtight, the pressure within the system should remain constant. If there are any leaks or defects, the pressure will drop over time.
5. Analysis – If pressure changes are observed, the system can then be analyzed to determine the source of the problem. This can involve using techniques like gas detection or vacuum decay testing to pinpoint the exact location of any leaks or defects.
Why is Vacuum Pressure Testing Important?
Vacuum pressure testing is an important tool for ensuring the safety and reliability of a range of products and systems. Here are just a few reasons why vacuum pressure testing is important:
1. Safety – Many systems that rely on vacuum pressure, such as refrigeration systems or pressurized containers, can pose significant safety risks if they are not properly sealed. Vacuum pressure testing can help identify any potential leaks or defects that could compromise the safety of the system.
2. Efficiency – An airtight system can operate more efficiently than one with leaks or defects. Vacuum pressure testing can identify any areas where efficiency could be improved, helping to save energy and reduce costs.
3. Compliance – Many industries have specific regulations or safety standards that require vacuum pressure testing. By conducting regular testing, companies can ensure that they are meeting these requirements and avoid potential fines or legal issues.
4. Reliability – Whether it's a medical device or a spacecraft, reliability is critical in many industries. Vacuum pressure testing can help identify any potential issues before a product is released, ensuring that it meets the high standards of reliability that are expected in these industries.
In conclusion, vacuum pressure testing is an important process that helps ensure the safety, reliability, and efficiency of a range of products and systems. By creating a vacuum within a sealed system and monitoring changes in pressure over time, potential leaks or defects can be identified before they become a major problem. For companies in regulated industries, regular vacuum pressure testing is often a requirement, and it can be a key factor in ensuring compliance with safety standards and regulations.